commentary Commentary
Commentary: Spate of workplace deaths and what needs addressing in Singapore's safety culture
The 11 deaths in February were three times more than the monthly average of 3.8 workplace fatalities over the last five years, says Associate Professor Goh Yang Miang of NUS.
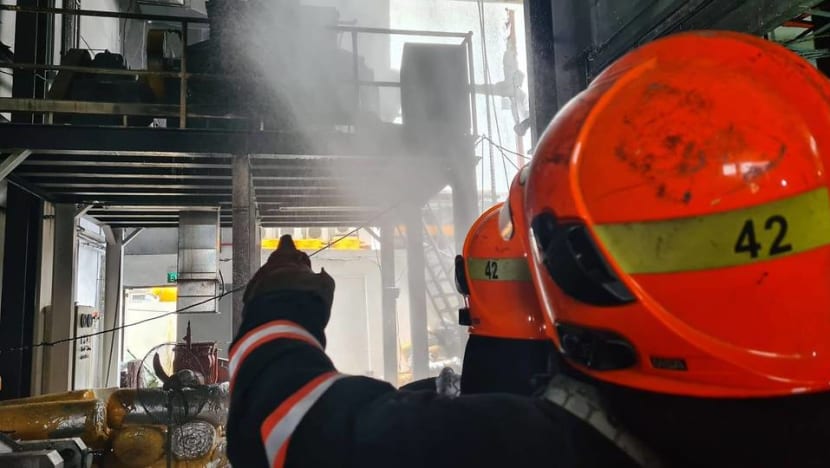
SCDF firefighters responding to a fire at 32E Tuas Avenue 11 on Feb 24, 2021. (Photo: Facebook/SCDF)
SINGAPORE: Singapore’s weakest link in the fight against COVID-19 proved to be infections spreading in migrant worker dormitories. As a result, all work involving these men ground to a halt.
A year later, the economy is set to grow by 4 to 6 per cent after a slowdown in 2020.
The relief at restarting the engine however has been overshadowed by a spate of bad news. One, an explosion in Tuas killing three workers and leaving five in critical condition on Thursday (Feb 25) and the death of a lift technician after being trapped in a North Bridge Road building lift shaft two days later.
Worse, it was just barely three days before the Tuas incident that Senior Minister of State for Manpower Zaqy Mohamad said the seven workplace fatalities in February in Singapore were "extremely alarming".
READ: Tuas explosion: 3 workers die from injuries, 5 in critical condition
READ: Technician dies after getting trapped in lift shaft in North Bridge Road building
Just two months ago, Singapore saw a series of fatal accidents in November and December 2020, a period of lower level of business activities.
One death is one too many. Yet these 11 deaths in February were three times more than the monthly average of 3.8 workplace fatalities over the last five years, according to the Workplace Safety and Health Report.
Migrant workers form the bulk of such fatalities but several Singaporeans and permanent residents were also killed in February’s fatalities.
Pinpointing what went wrong exactly may be premature when investigations are ongoing.
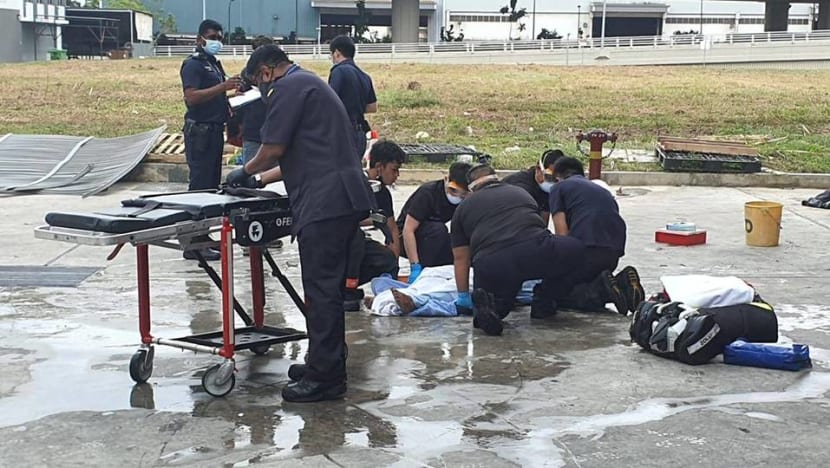
But the Workplace Safety and Health Council has highlighted how workplaces in some of these cases failed to carry out adequate risk assessments, with some cases seeing the untrained and unauthorised use of machinery, including forklifts. These findings will be worth pouring through to derive lessons for companies.
RESPONSIBILITY CANNOT LIE WITH WORKERS
Individual responsibility and personal ownership over safety are often cited as keys to a safe workplace. Research bears this out when about 80 per cent to 90 per cent of accidents can be attributed to the unsafe behaviours of workers.
But workers’ behaviours are influenced by other factors including workplace safety policies and processes, the organisation’s safety culture, leadership emphasis and management behaviour.
Recognising this, when Singapore debated the ground-breaking Workplace Safety and Health Act almost 15 years ago in Parliament, Dr Ng Eng Hen, the then-Manpower Minister emphasised how a combination of factors could prove a dangerous mixture leading to an accident.
He said: “On a day-to-day basis, safety may be the last thing on the minds of management and workers on the ground. There are deadlines to meet, monotony, apathy or lethargy to overcome, a lack of professionalism and training, unclear lines or no lines of accountability, and poor management.”
That is also why the Workplace Safety and Health Act deliberately focuses on the importance of comprehensive risk assessment, industry ownership, and penalties to deter risk-taking behaviour.
Policymakers are well aware that companies are ultimately responsible for safety and the buck cannot be passed to workers.
SAFETY IS A HYGIENE CHALLENGE
There is much at stake for companies. With major business disruptions last year, 2021 is poised to be a year of recovery. They should not spare any effort in seizing new opportunities and getting business out.
Yet in the haste to recover, many organisations, under tremendous work pressure and facing a lack of resources, may push safety boundaries by spending less time on ensuring work resumes in a safe manner and supervising operations.
Worse, they may take riskier actions to improvise work methods in unsafe manners and cut concerns on safety and health rules.
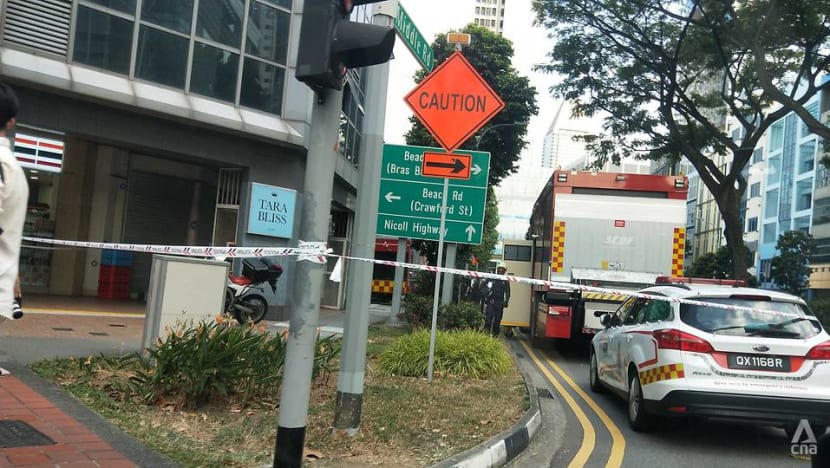
In 2014, a group of five construction workers and a foreman improvised a loading platform suspended by a tower crane to lift an air compressor. The trouble was the loading platform was not designed to transport the air compressor. The air compressor rolled away from the edge of the building and threw two workers off.
The negligence of a project manager and a workplace safety and health officer in another case in 2017 resulted in a construction worker being struck by a steel plate, pinning him against another.
READ: The impact of workplace accidents: Victims struggle with debt and changed lives
Both failed to ensure proper risk assessment and implementation of safe work procedure, resulting in workers resorting to unsafe methods of work.
Professor James Reason who pioneered the often used Swiss Cheese model of safety, had highlighted how organisations that push safety boundaries are like human bodies infected by pathogens, which increase the likelihood of the hosts developing serious disease.
His point that unsafe management practices do not result in accidents and ill health immediately, but can provide fertile ground for accidents and ill health to happen should be taken seriously.
LESSONS AND REMINDERS FROM 2004
To be fair, Singapore has made tremendous improvement in our workplace safety and health performance since 2004, with the collapse of the Nicoll Highway, the accident at Fusionopolis and fire at Keppel Shipyard prompting a soul-searching in Singapore on how safe our work sites were.
The ongoing pandemic and its knock-on effects on the economy are a test of the resilience of our safety system, culture and leadership at all levels and whether they can stand up to the need for financial survival of businesses.
Since COVID-19 is a major disruptor, we cannot assume that the previous improvements in safety culture are still intact.
The committee of inquiry (COI) for the Nicoll Highway collapse in 2004 emphasised important safety lessons worth revisiting today.
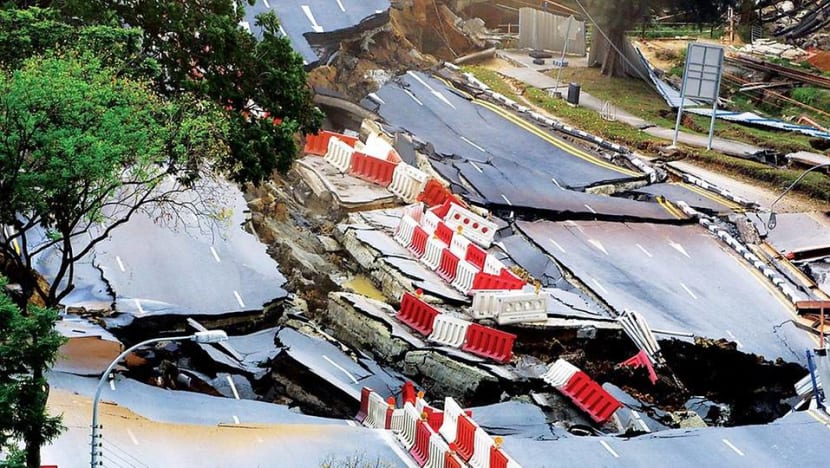
The report recommended that safety measures should be continuously watched, worried about, tuned and adjusted, while guarding against an overly simplistic analysis of incidents that blames only operators.
To prevent fatalities and poor safety performance from becoming a norm in the current challenging economic climate, the Ministry of Manpower has already stepped up on their inspections and interventions by adding 300 inspections in high-risk industries. This is on top of the 400 inspections after the spate of accidents late last year.
More importantly, organisations must be reminded of past painful lessons and take concrete actions to safeguard safety across business planning functions and operations.
READ: Commentary: Maybe private-hire drivers and food delivery riders don’t want full-time jobs
For example, executives purchasing equipment must consider feedback from frontline staff regarding the safety of the equipment. In contract work, besides considering the accident rates of contractors, their safety management system, competency and attitude should also be assessed.
The construction sector should increase its adoption of technologies to help make work safer. Computer vision and sensors can alert workers when they are near dangerous equipment and areas.
Prefabrication can reduce the need for workers to work at heights for long periods. Drones can remove the need for workers to conduct inspections in confined spaces or at heights.
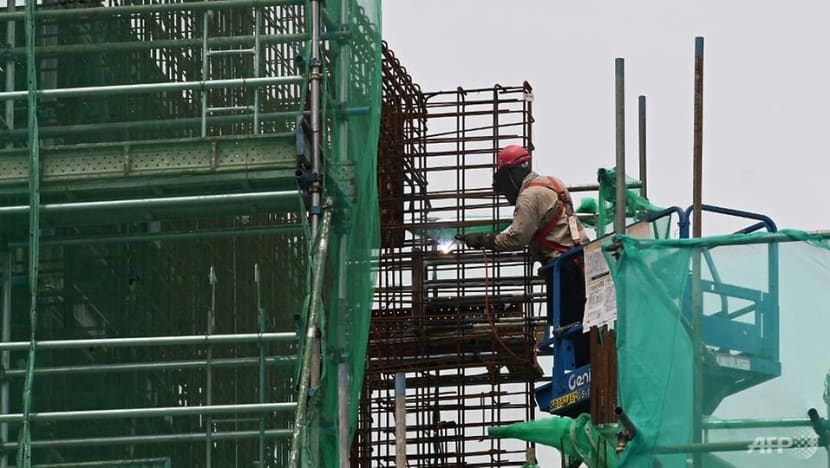
Supervisors must also engage frontline workers in safety processes like risk assessments, safety meetings, safety suggestion schemes, safety inspections, and safety training to demonstrate management seriousness about their safety and health and be empowered to make a difference.
Workers must know they have recourse to authorities when asked by managers to engage in unsafe work, with whistle-blowers protected by the Workplace Safety and Health Act.
In Parliament on Friday (Feb 26) during the Budget debates, NTUC Assistant Secretary-General Melvin Yong suggested having a workplace safety and health representative in all companies.
This could get workers and companies more engaged in safety management, that improves safety culture.
However, the key to the success of any safety measure remains the commitment of company leadership.
Perhaps the good arising from the recent spate of accidents is the reminder that safety management is like riding a bicycle on an upslope, you simply cannot stop pedalling.
SIGN UP: For CNA’s Commentary weekly newsletter to explore issues beyond the headlines
Dr Goh Yang Miang is Associate Professor with the Safety and Resilience Research Unit (SaRRU) at the Department of Building, National University of Singapore, where he is also the Director of the Centre for Project and Facilities Management. He was previously Council Member and Chairman of the Health and Safety Engineering Technical Committee at the Institution of Engineers, Singapore.​​​​​​​